This weekend was occupied with lots of little things inconveniently scattered throughout the two days, so I never really got a rhythm in the shop. I managed to sharpen all my chisels, and started on my plane blades. One day I would like to be able to sharpen as I use them and not feel like I have to dedicate hours to sharpening everything I own....maybe next week.
What I did do (for the second weekend in a row) was brew a beer. I got a recipe from Brady for his IPA, and he had a bunch of extra supplies, so this beer only cost a pack of yeast. Looks like I owe him a beer. For those that haven't take a brewery tour, the basics behind brewing beer are: harvest some grains, let them start to germinate so they are loaded with starch, then toast them. You now have malted barley.
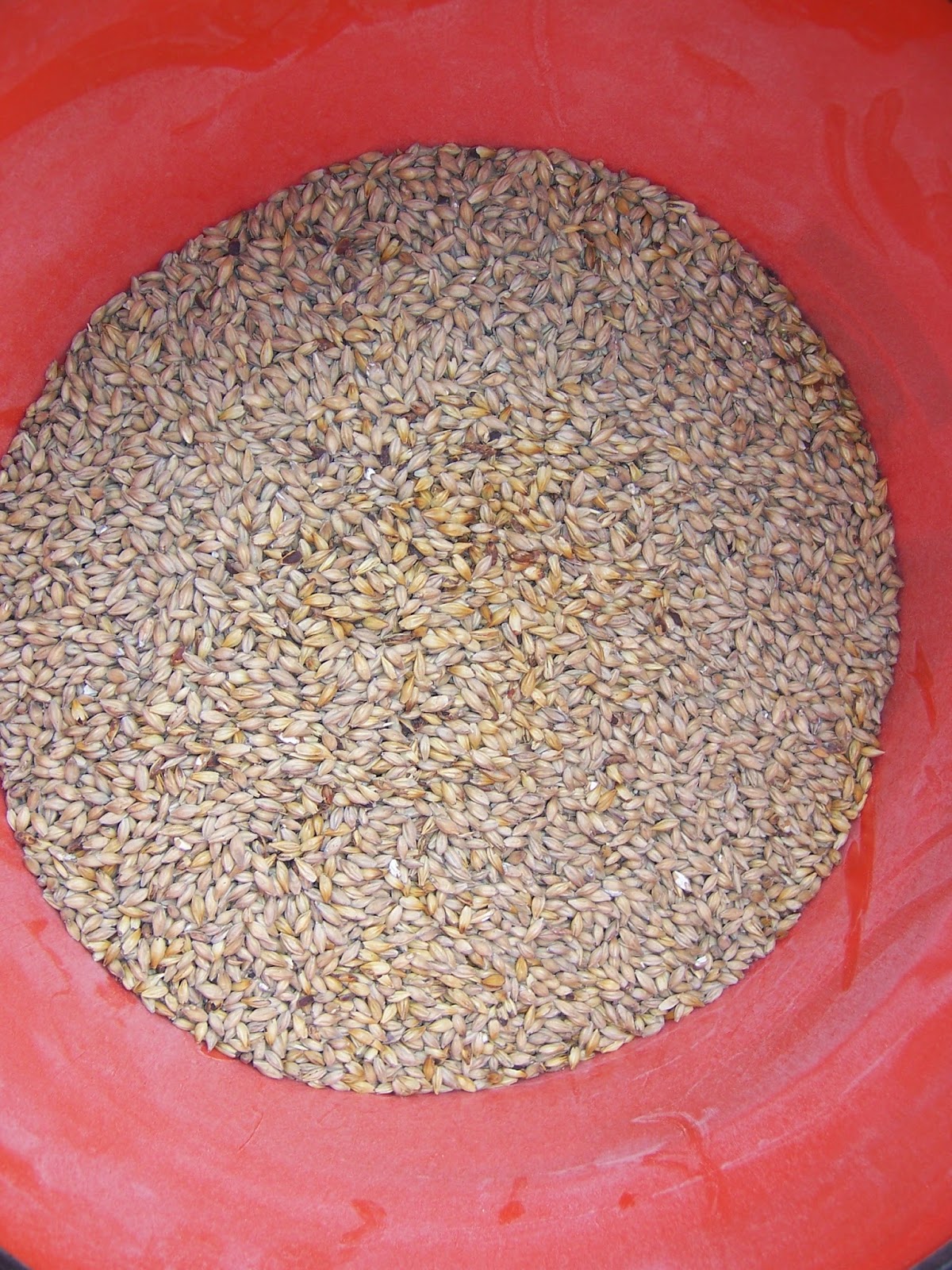 |
Malted barley in a bucket |
Break open the kernels to get at the endosperm.
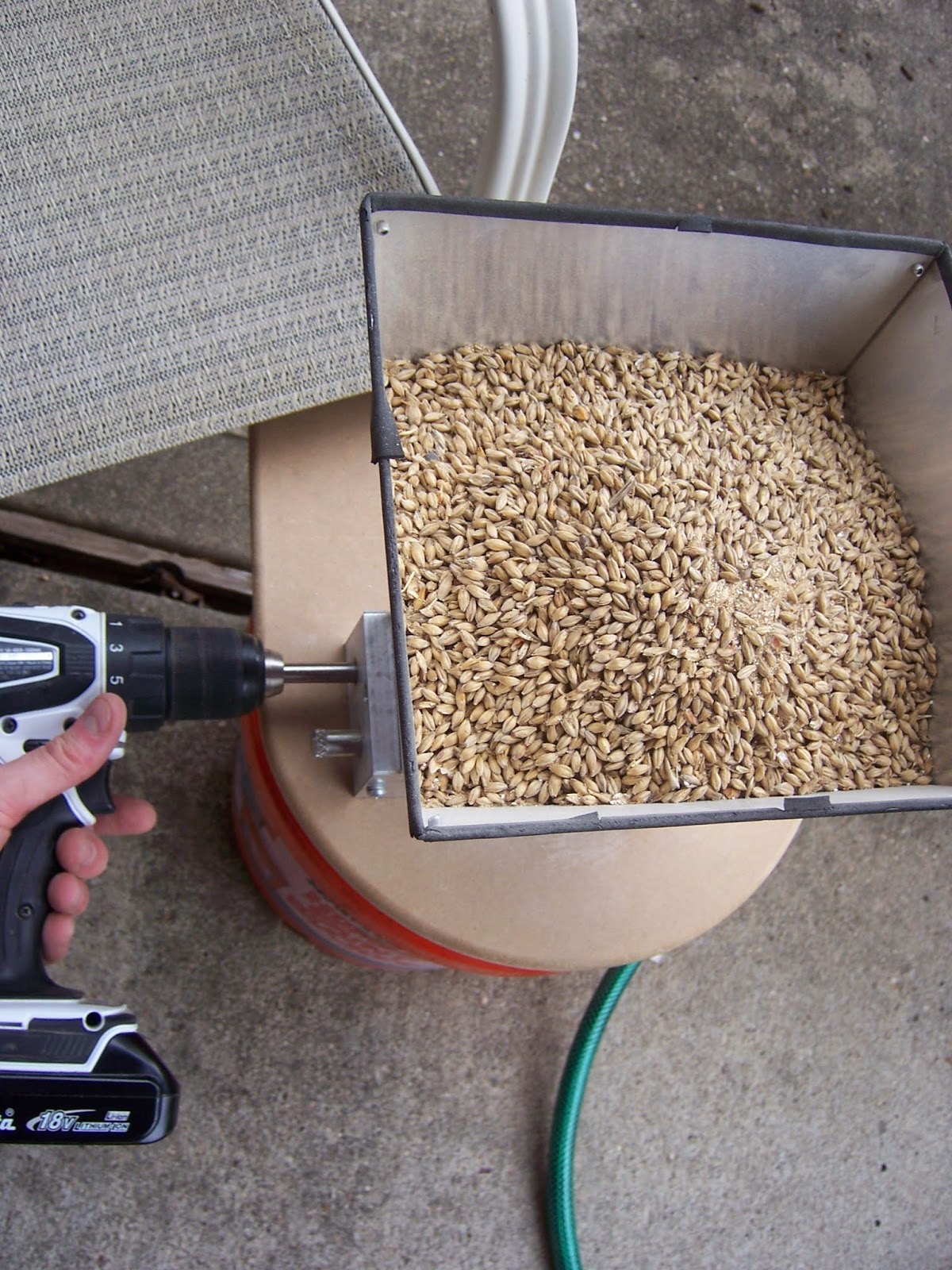 |
I usually get it crushed at the store but this time I borrowed Brady's grain mill, |
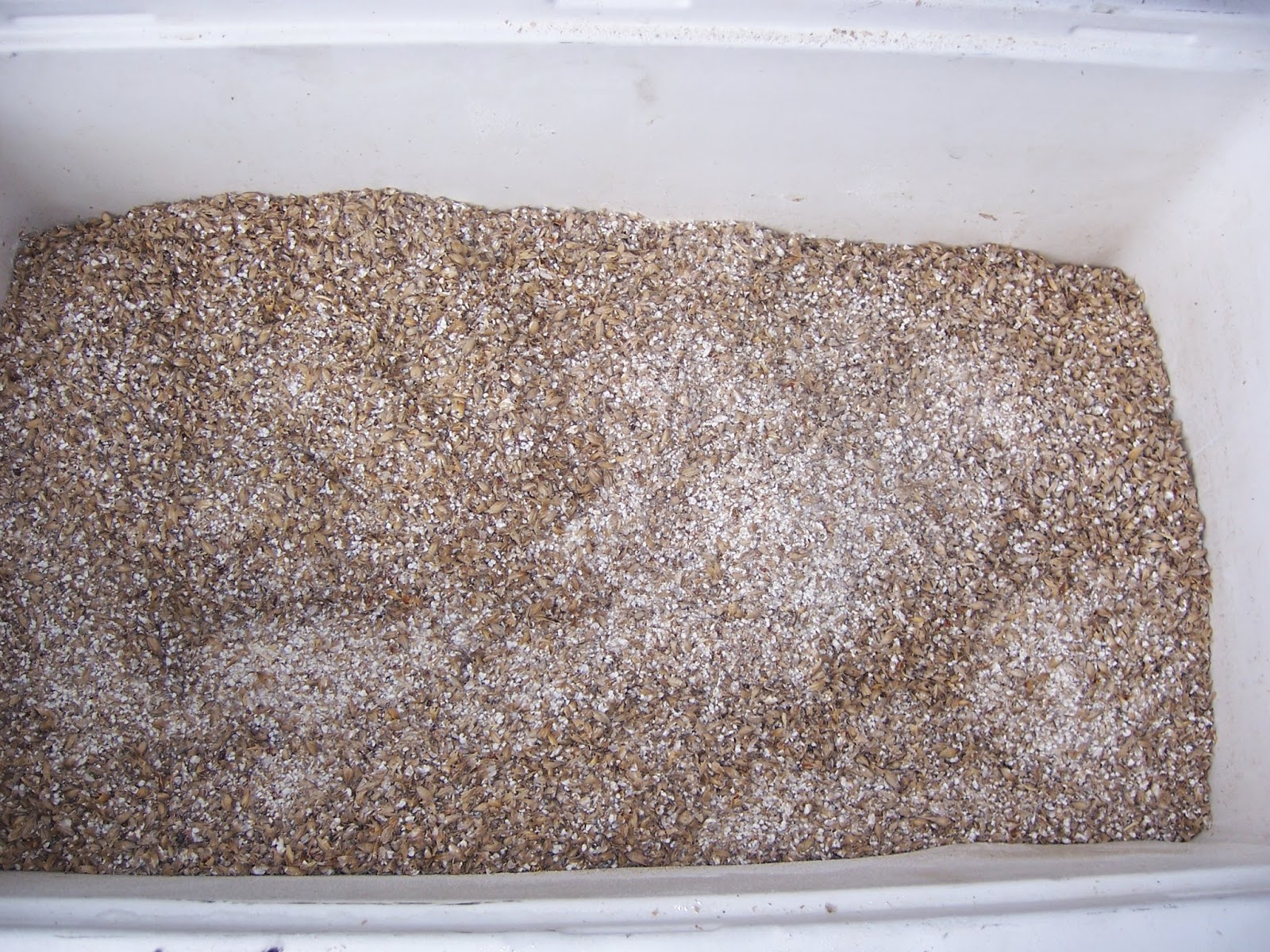 |
Broken husks and crushed endosperm |
I put the grain in my mash tun, which is a cooler with some slotted copper pipe at the bottom. The pipe lets the sweet liquor through, stopping the grain.
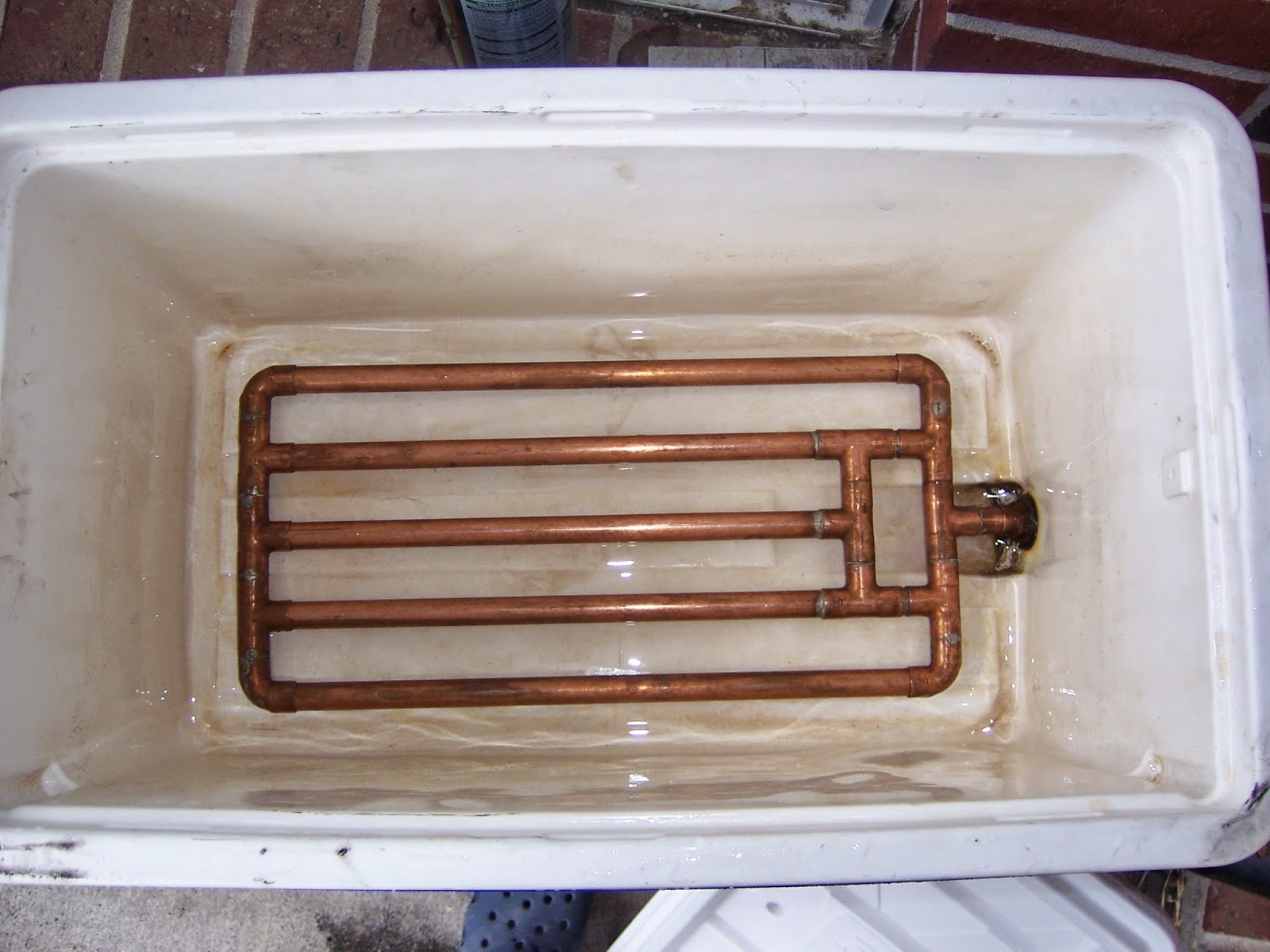 |
The slots are sawn in the underside of the pipe |
Add some hot water and let it soak at 153 degrees for an hour to convert the starch to sugar.
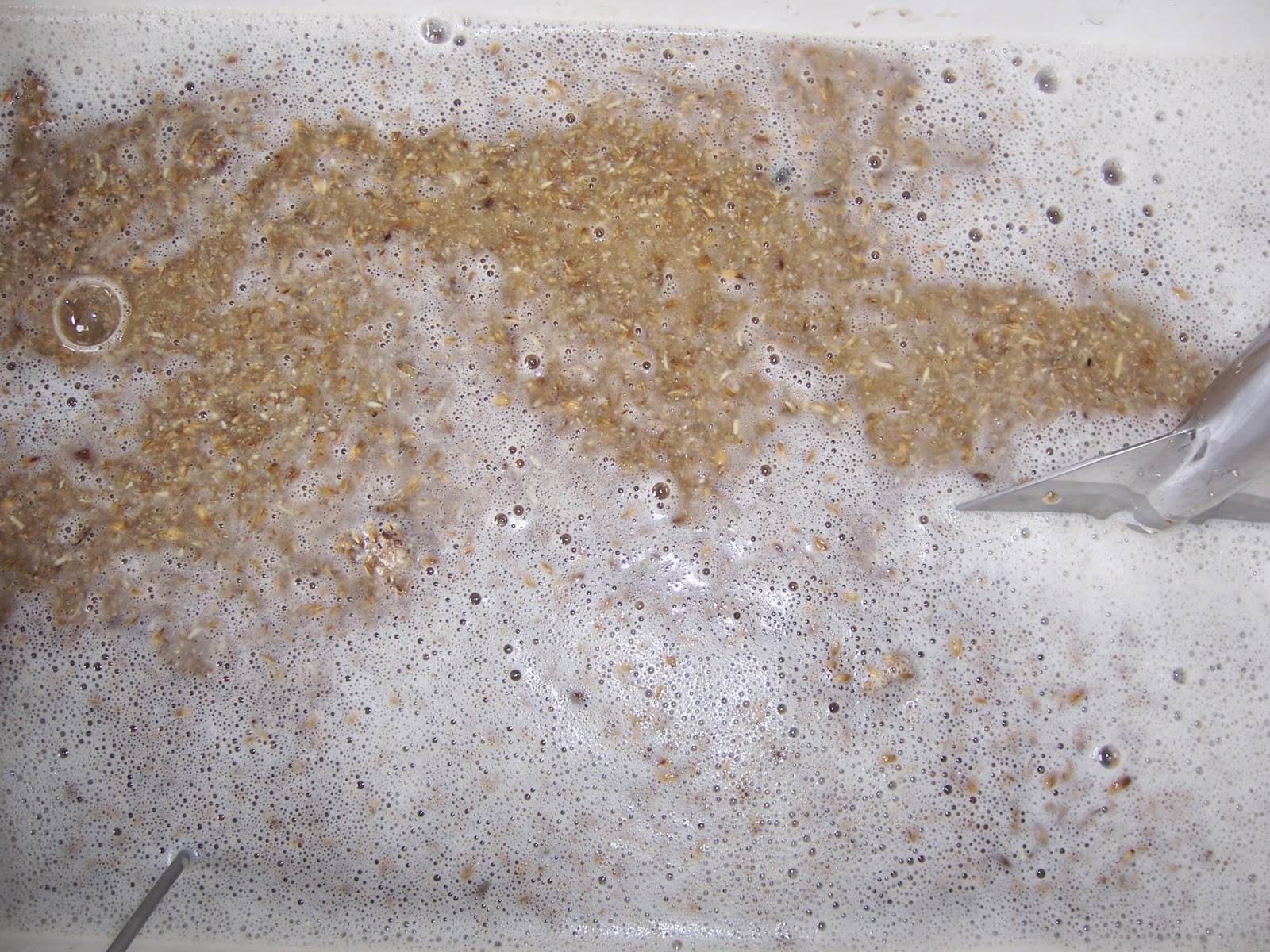 |
This smells great, by the way. |
I batch sparge my beer, because I haven't figured out and made a fly sparging apparatus. So I drain all the sweet liquor and then pour in some 170 degree water to basically wash the grains of any remaining sugars.
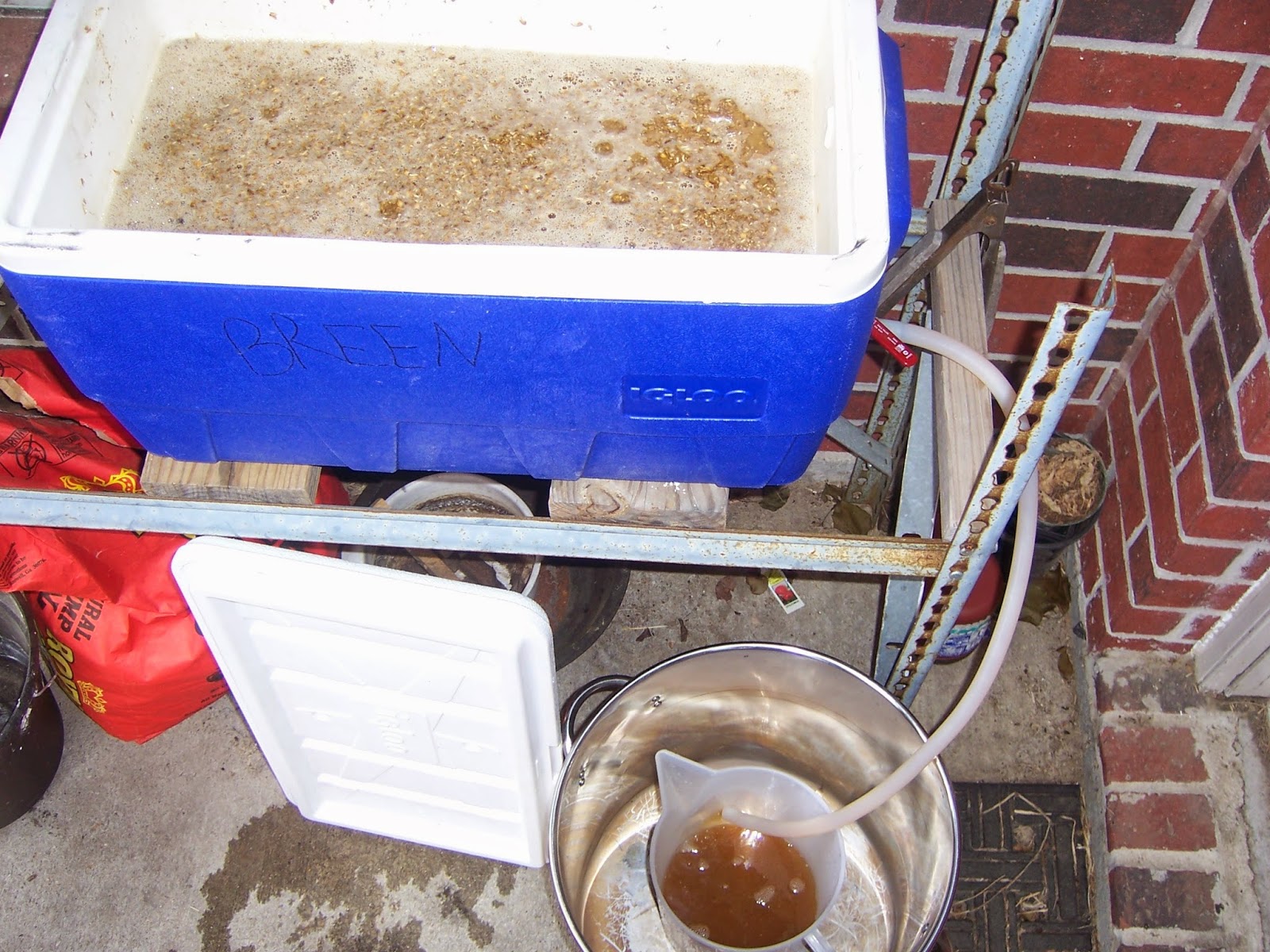 |
The first few liters is usually cloudy so I pour that back in, and then it pours clear. |
Now boil for an hour or so, and add hops at whatever your recipe calls for. When added earlier in the boil, they add more bitterness, versus later, which tends to add more aroma.
 |
This also smells fantastic. |
This needs to cool to somewhere between 65-75 degrees before the yeast are added so they survive. To do this I made a counterflow wort chiller. It is 25 ft. of copper tubing with some solid core wire wrapped around it (and soldered in place) inserted into a garden hose. The wort flows through the copper tubing, and then water flows between the tubing and the hose in the opposite direction. The wire helps disturb the water flow, so that its not always the same water in contact with the copper tubing. This allows me to open the valve on the kettle all the way, and as the wort drains into the carboy is is instantly cooled to whatever the water temperature is ~70. It takes about 10 minutes to transfer.
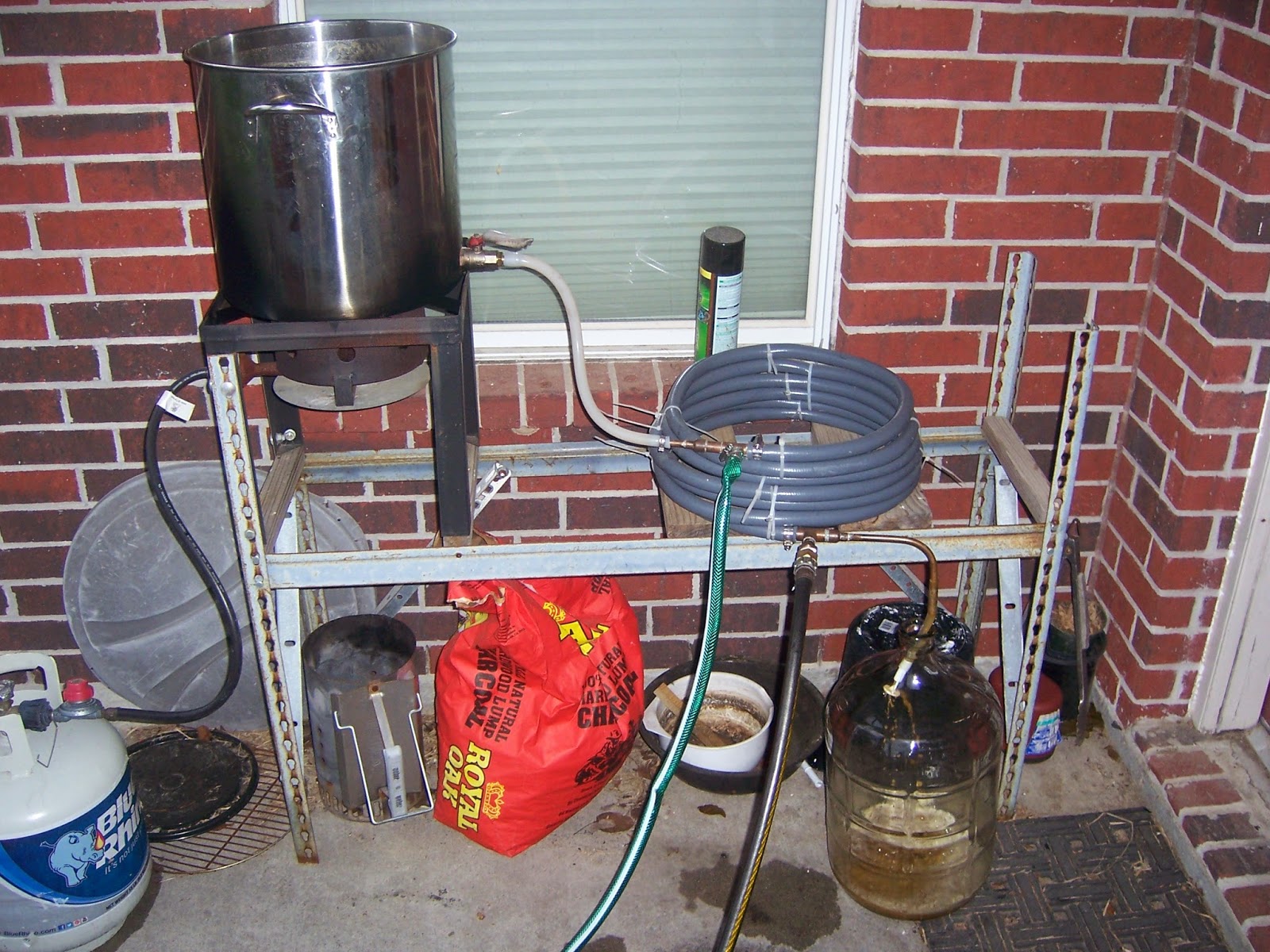 |
Draining and cooling the wort. |
Next is to add the yeast. I like to transfer the beer from one carboy to another after about 3-6 days. Then it sits in the secondary for the remainder of 2 weeks, or whenever I get a chance to keg it.
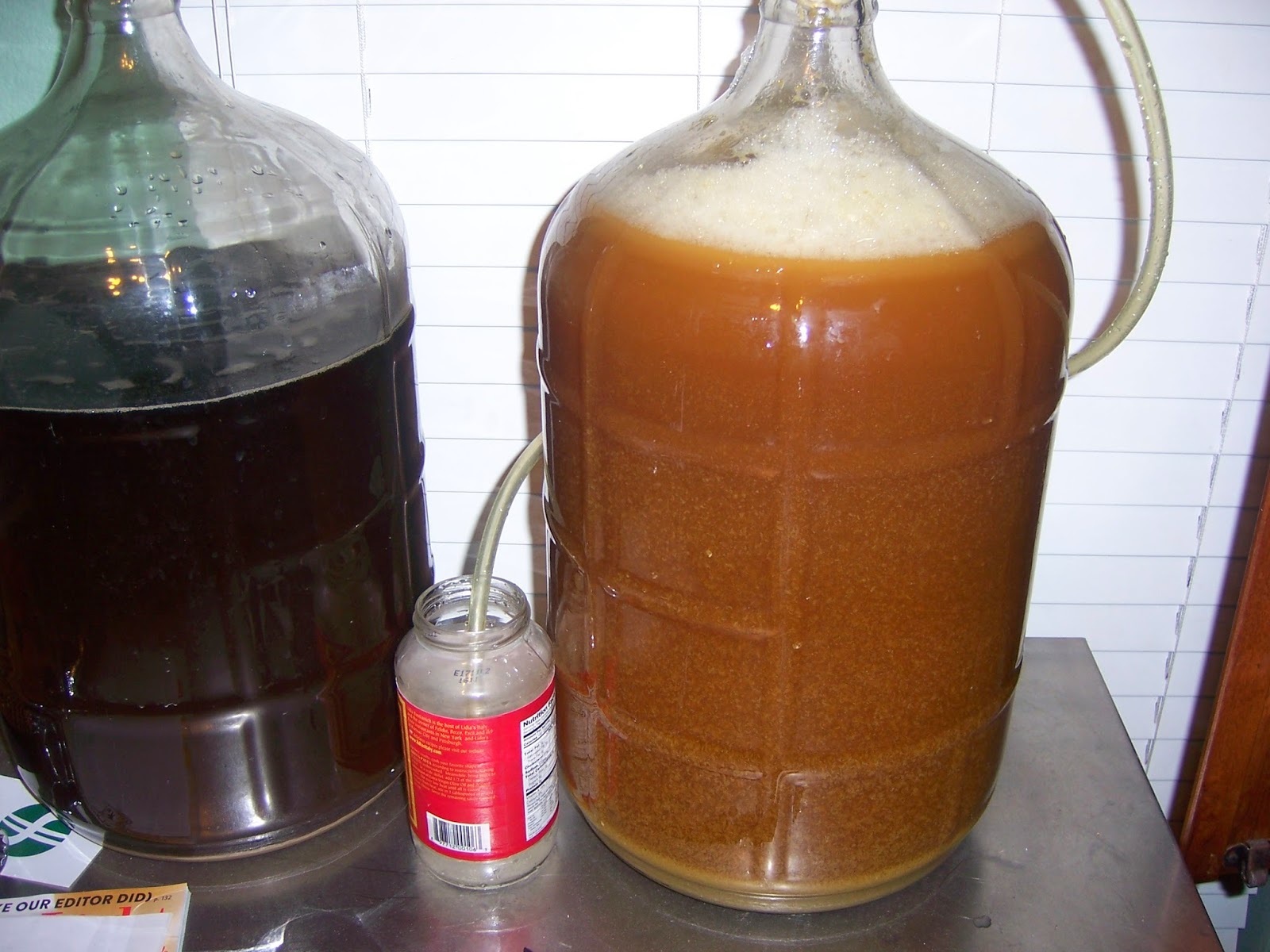 |
Just a few weeks till beer. |
My process and equipment isn't the prettiest, but it brews a good beer, and I have gotten it down to where I only need to check on it every 20-60 minutes depending on where I am in the process. From heating the water to putting my stuff away takes about 4 hours.